Entrevistas
Necesidad de velocidad: Rome Snowboards acelera el desarrollo de productos con la impresión 3D SLS
16 Septiembre 2022
Fabricación
Entrevista

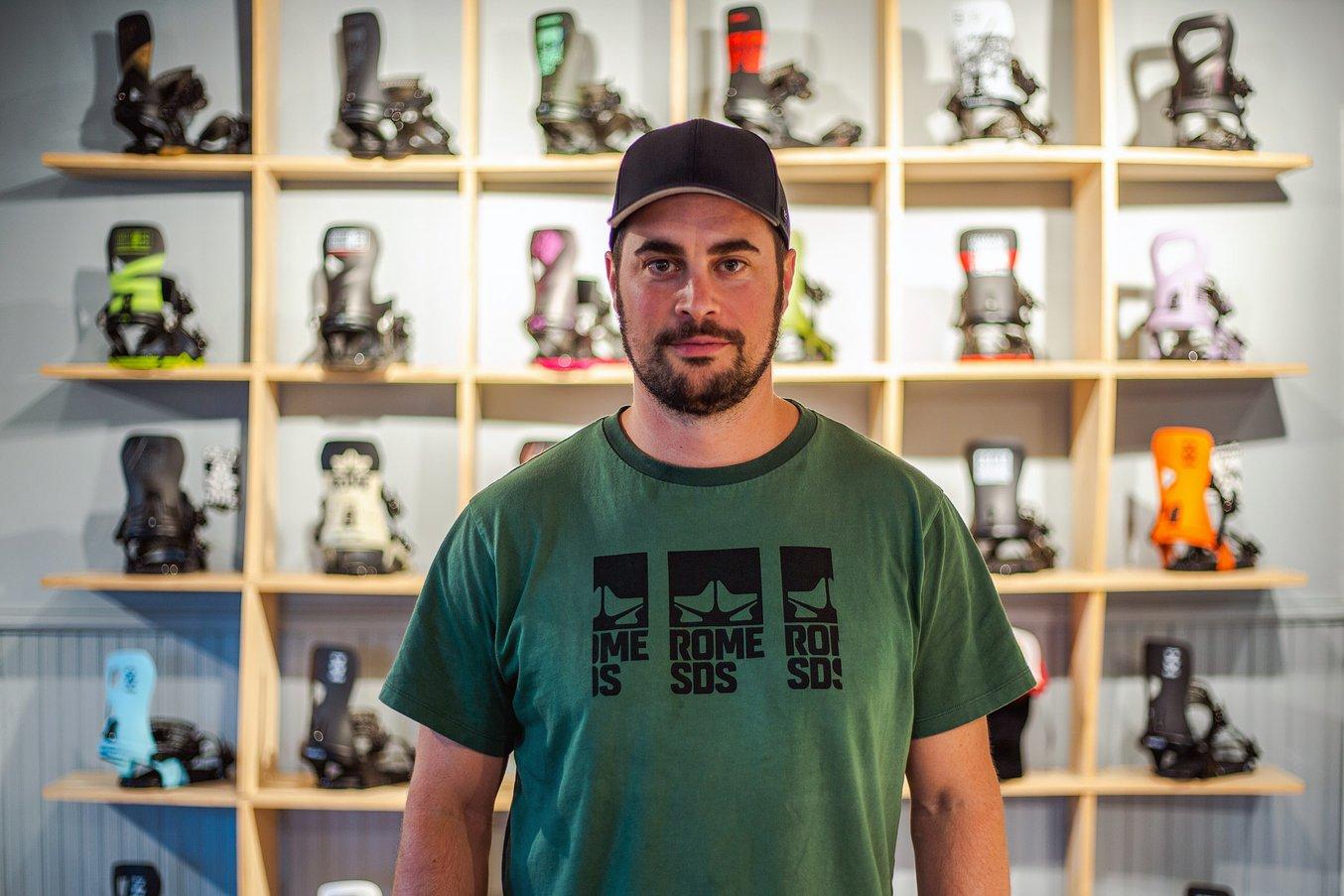
Justin Frappier, diseñador de productos de Rome Snowboards, puede diseñar, crear prototipos e iterar todos los días gracias a la impresión 3D SLS en su empresa.
Siempre intentamos hacer algo que no se haya hecho antes… Ya estamos viendo el ROI, lo vimos en los primeros cinco meses simplemente acelerando la creación de prototipos.
Justin Frappier, diseñador de productos de Rome Snowboards
Desde su invención en la década de 1960, el deporte del snowboard se ha asociado con la rebeldía; sus estrellas juveniles y descaradas, su ropa holgada y sus llamativos saltos lo convierten en el hermano menor punk del elegante mundo de los deportes de invierno, mientras que las similitudes de estilo con el surf y el monopatín ayudan a atraer a las mismas multitudes y fortalecer su imagen de contracultura.
El snowboard nació del deseo de hacer las cosas de forma diferente, y el equipo necesario es un reflejo muy técnico de ese espíritu. Las empresas de equipos de snowboard buscan constantemente nuevas formas de mantener a los snowboarders en la montaña durante más tiempo con equipos fiables, resistentes y cómodos que puedan soportar una temporada completa en las pistas. Para acelerar su proceso iterativo y mantener un flujo constante de nuevos diseños innovadores, los fabricantes están recurriendo a la impresión 3D interna. Rome Snowboards, una pequeña empresa de diez personas de Waterbury, Vermont, tiene un lema: «All Ways Down». Esto se aplica a su espíritu en la montaña y a su proceso de desarrollo: el diseñador de productos Justin Frappier siempre está buscando nuevos procesos y métodos para crear fijaciones y botas. El objetivo general de Rome es generar un equipo que permita realizar recorridos más largos y cómodos y que pueda soportar la torsión y el impacto generados durante los saltos, los giros y los toboganes. Con la incorporación de una impresora 3D de sinterización selectiva por láser (SLS) Fuse 1, Rome ha podido innovar más rápidamente y probar sus prototipos en la montaña, lo que ha permitido un proceso iterativo más riguroso. «Siempre intentamos hacer algo que no se haya hecho antes… Ya estamos viendo el ROI, lo vimos en los primeros cinco meses, simplemente acelerando la creación de prototipos», dice Frappier.
Rome ya crea algunos de los productos más respetados de la industria, obteniendo críticas de medios como White Lines, que eligió las fijaciones Vice de Rome para su lista de los 100 mejores productos de snowboard de 2021-2022, diciendo: «Son unas fijaciones sumamente versátiles que combinan una tecnología probada y fiable con algunas características de primera calidad… Rome ha dado en la diana con la última versión de su superventas Vice».
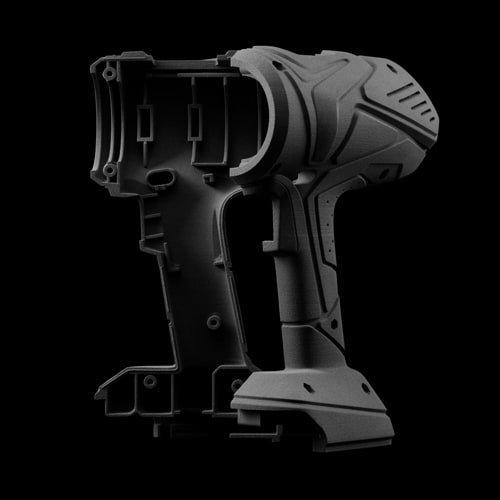
LIBRO BLANCO
Introducción a la impresión 3D por sinterizado selectivo por láser (SLS)
¿Busca una impresora 3D para crear piezas resistentes y funcionales? Descargue nuestro libro blanco para saber cómo funciona la impresión SLS y por qué es un proceso de impresión 3D muy popular para la creación de prototipos funcionales y la producción final.
De los prototipos a la producción en serie
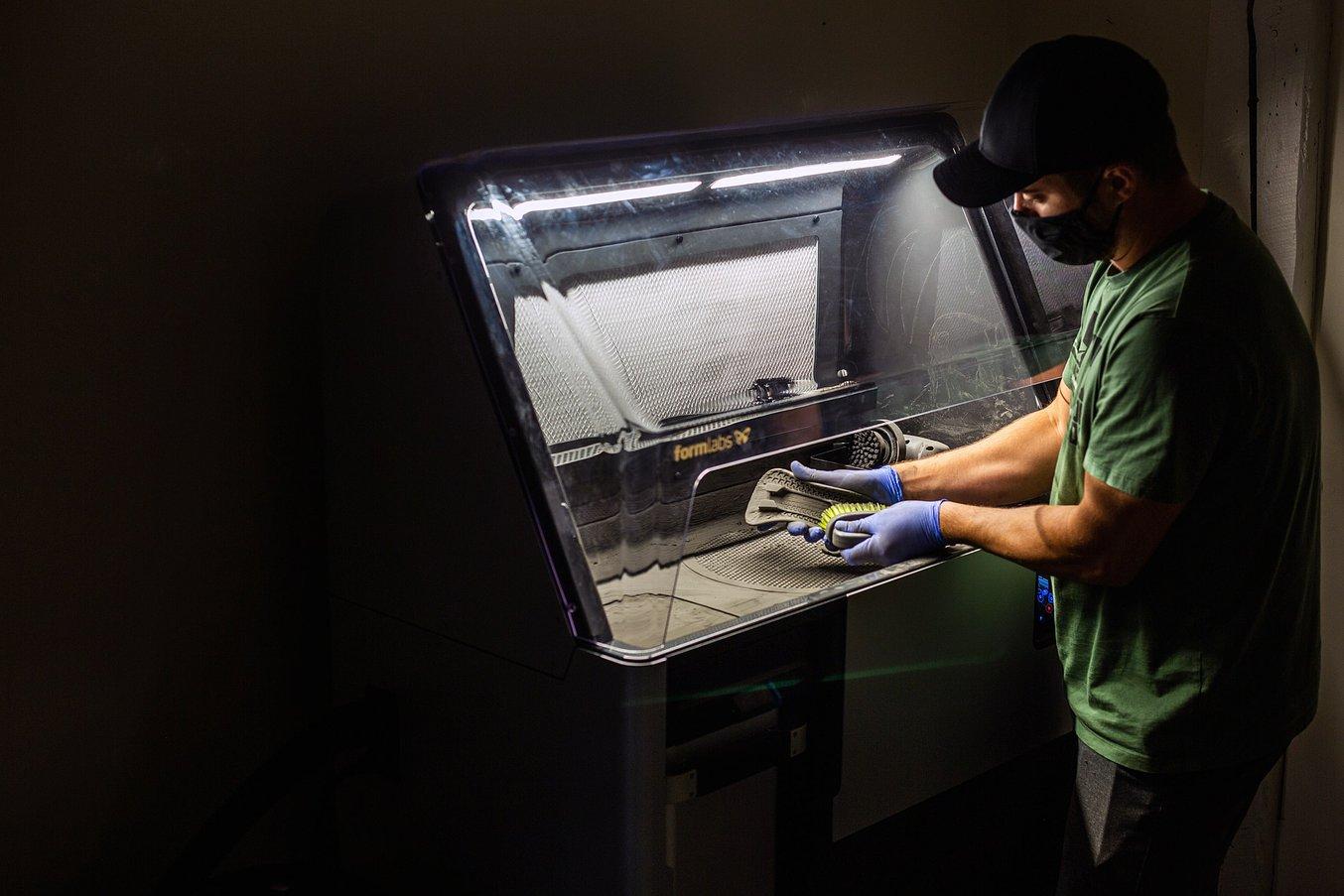
La Fuse Sift agiliza el proceso de posprocesamiento y reciclaje de polvo, liberando el tiempo de Frappier para tareas más intensivas de diseño.
Además de esculpir la arcilla, el equipo había encargado algunas piezas impresas en 3D al otro lado de la frontera, en Montreal. Aunque el coste no era desorbitado, el tiempo de espera afectó a su capacidad de diseñar a la velocidad a la que estaban acostumbrados. «Estábamos en una cola de espera con otras empresas, así que la velocidad de desarrollo dependía de que nos devolvieran las piezas», dice Frappier.
Para una pequeña empresa como Rome, conocida por tener componentes de encuadernación altamente personalizables, los retrasos en el desarrollo la sitúan en desventaja frente a los grandes fabricantes. Su fortaleza radica en su capacidad de iterar, obtener rápidamente las aprobaciones internas y crear productos únicos y «pioneros» en el sector, como sus tecnologías patentadas AuxTech, PivotMount y AsymWrap.
«Solamente tenemos la Fuse 1 desde hace unos seis meses, pero enseguida vimos el beneficio de tenerla en las instalaciones. Estuvimos trabajando en hebillas durante unos seis meses más o menos. Imprimimos una hebilla, la montamos, vimos cómo encajaba, los problemas y las incidencias. Fue muy útil poder utilizar la impresora, imprimir una pieza y, a la mañana siguiente, comprobarla, montarla, revisarla, ensamblarla, hacer correcciones y volver a fabricarla al día siguiente», dice Frappier.
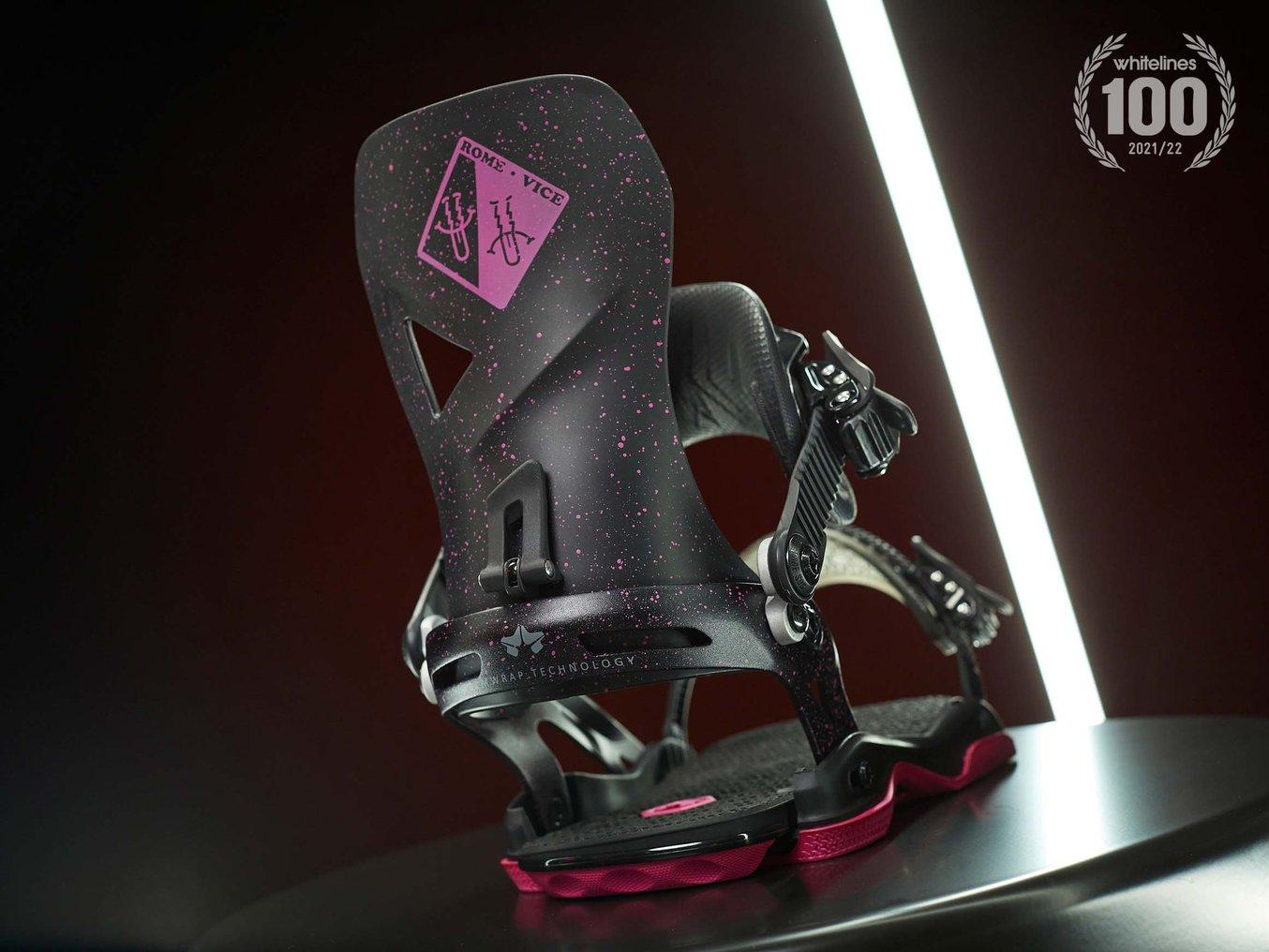
La galardonada fijación Vice, fotografiada aquí en la reseña de White Lines. Foto por cortesía de White Lines.

LIBRO BLANCO
Subcontratación frente a la internalización: ¿Cuándo tiene sentido llevar la impresión 3D de SLS interna en la empresa?
En este libro blanco, evaluamos la propuesta de valor de traer las impresoras 3D SLS interna a la empresa, en comparación con la subcontratación de piezas SLS de una empresa de servicios.
Diferentes estilos para diferentes personas
Pequeño impacto, gran rendimiento
Somos una empresa tan pequeña comparada con otros fabricantes de fijaciones. Sólo somos entre ocho y diez personas en la oficina de Waterbury y el hecho de que tengamos una instalación completa de impresión en 3D es bastante impresionante. Mucha gente cree que somos una empresa más grande. Eso es lo bueno de la Fuse 1, que está al alcance de muchas empresas pequeñas.
Justin Frappier, diseñador de productos de Rome Snowboards
Cuando los atletas y los distribuidores de equipos visitan la oficina de Waterbury, Frappier dice que la respuesta a la Fuse 1 ha sido abrumadoramente positiva. «Cuando la gente ve la impresora, se queda alucinada. Podemos llevar los diseños y mostrarles una pieza en ese momento, tanto a los atletas como a los representantes de ventas de los distribuidores de equipos. Así podemos obtener su opinión sobre la pieza antes de enviarla al utillaje», dice Frappier.
Cada vez más rápido en los prototipos funcionales
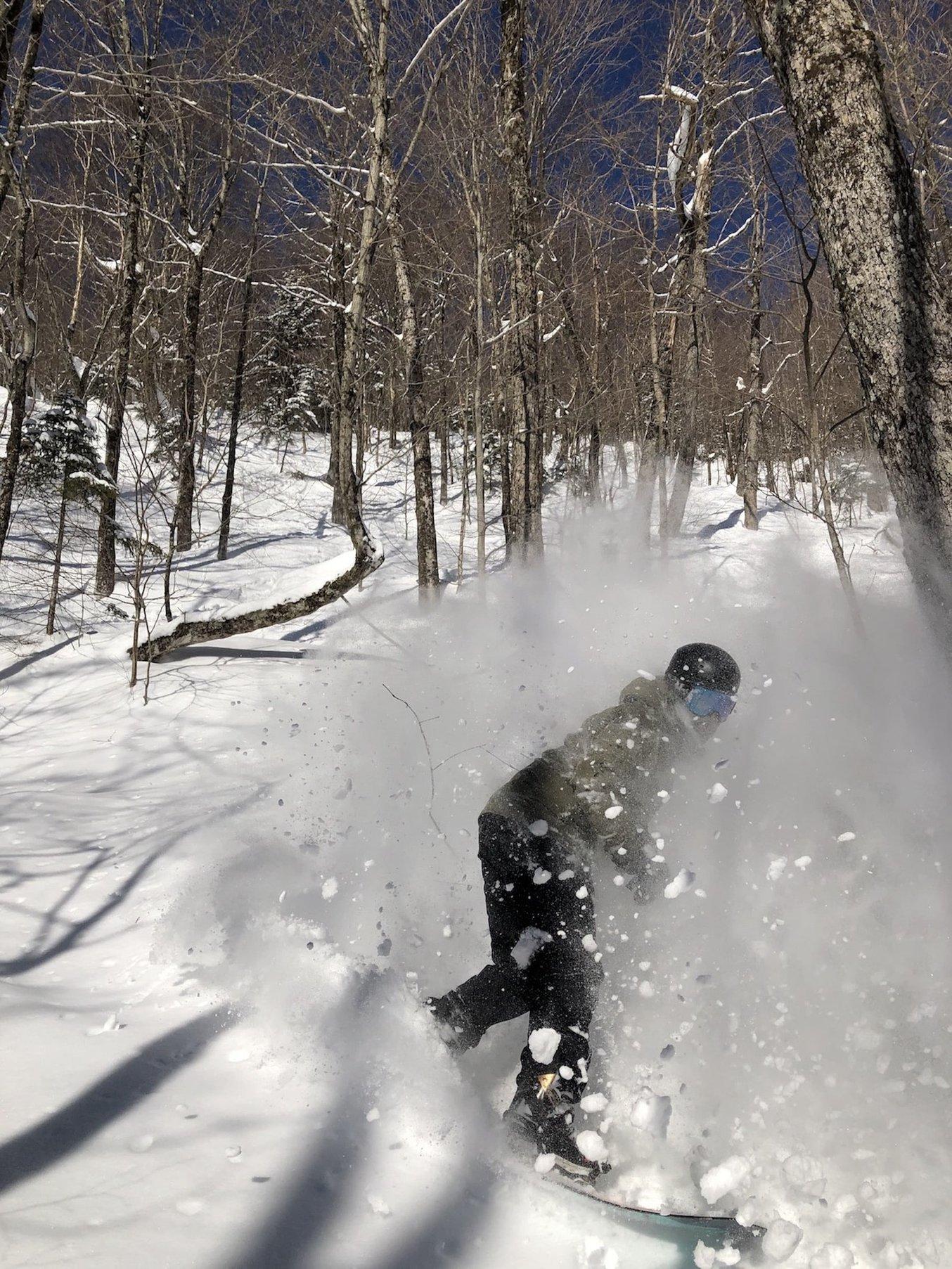
El principal argumento de venta era que podíamos montar las piezas impresas. Nunca habíamos podido hacer eso con otras piezas. La primera vez que lo hicimos fue con la base de la fijación y los componentes del chasis. En cada carrera íbamos más y más rápido, y aguantaban muy bien, se sentían muy bien. Ahora podemos imprimir, montar y volver a imprimir al día siguiente.
Justin Frappier, diseñador de productos de Rome Snowboards
Dar al equipo de diseño un control total sobre todo el proceso creativo, de pruebas e iterativo ha permitido a Rome Snowboards seguir ampliando los límites de lo que es posible con el equipo de snowboard.
«Hacemos cosas pioneras en la industria en todas las categorías. Siempre intentamos hacer algo que no se haya hecho antes, y sólo conseguimos mejorar. Ya estamos viendo el retorno de la inversión, lo vimos en los primeros cinco meses simplemente acelerando la creación de prototipos», dice Frappier.
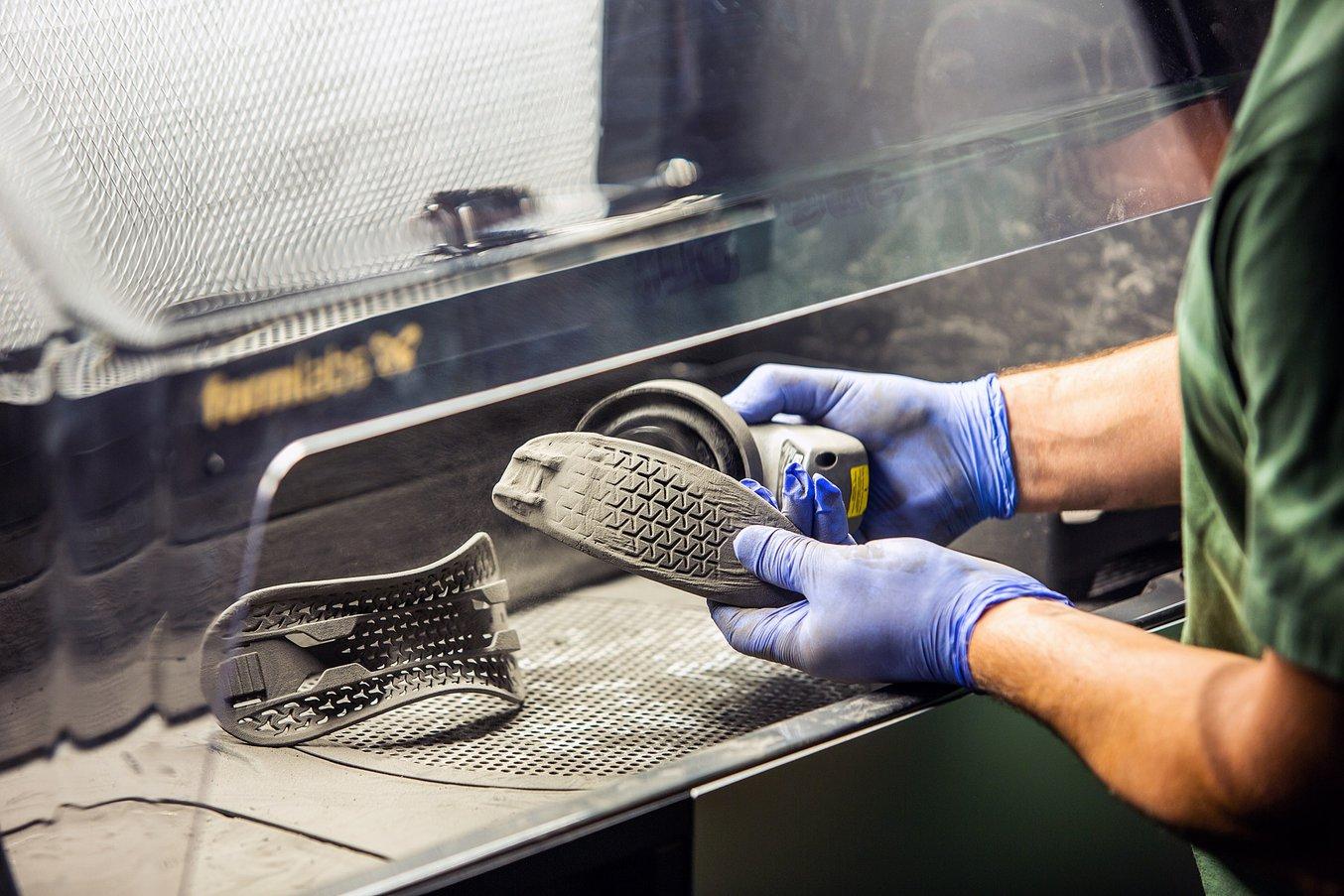
Eliminar y reciclar el polvo sin sinterizar es fácil en el flujo de trabajo independiente y optimizado de Fuse Sift.
Las impresoras de la serie Fuse permiten a los diseñadores probar funcionalmente sus productos e iterar con ellos sin tener que esperar las piezas de los proveedores. Para Rome Snowboards, la Fuse 1 ha acelerado el proceso de desarrollo en un orden de magnitud, lo que ha permitido a Frappier realizar «All Ways Down» mientras montaba fijaciones impresas en 3D. Para ver si la Fuse 1 puede hacer lo mismo con sus productos, pida una muestra o lea el libro blanco donde se compara el SLS interno con las piezas impresas por una empresa de servicios.